Overbend
Zajętość terenu
Zakotwienie
Geotechnika
WYBÓR METODY BEZWYKOPOWEJ
Techniki i technologie bezwykopowej budowy obejmują zbiór metod podziemnej budowy oraz rehabilitacji infrastruktury rurociągowej i kablowej, które charakteryzują się ograniczonym zakresem prac ziemnych i wykopów.
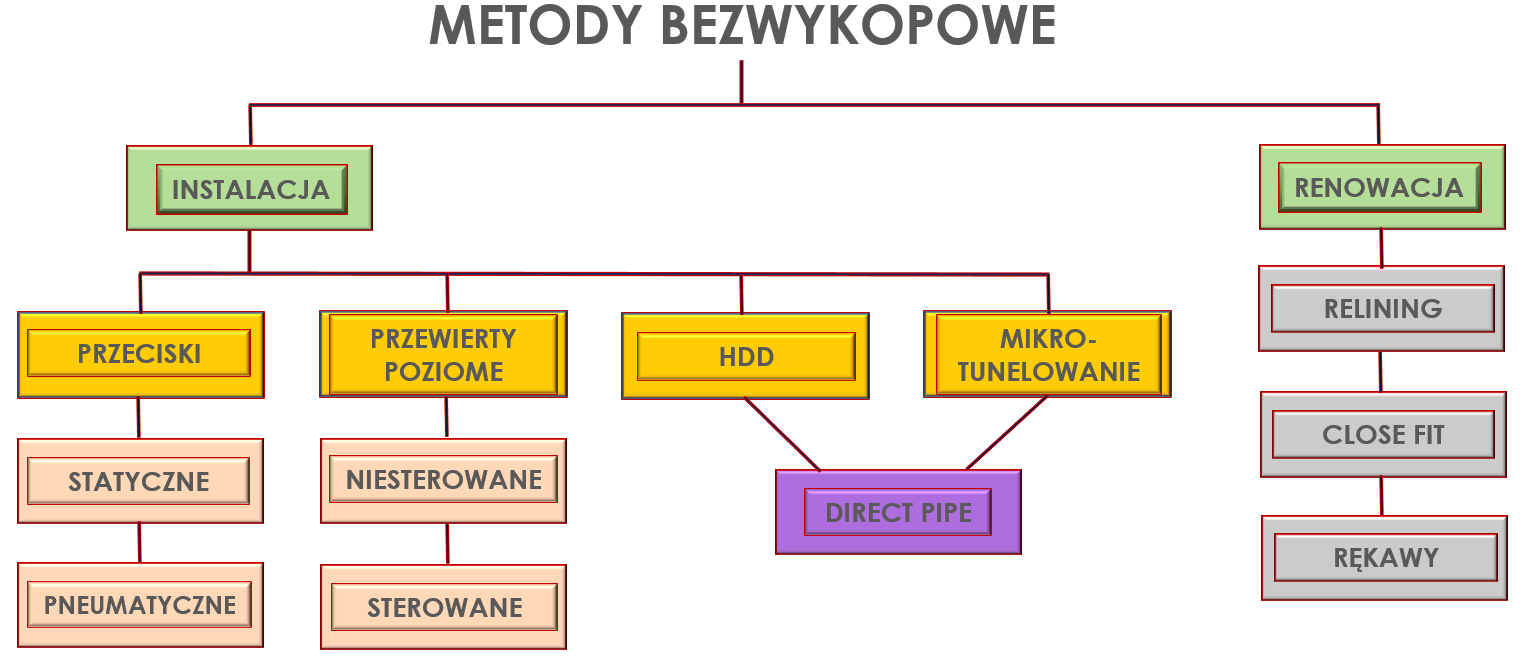
Podział metod instalacji nowych rurociągów można przeprowadzić ze względu na możliwość sterowania trajektorią podczas ich realizacji. Zgodnie z tym kryterium wyróżnia się metody sterowane i niesterowane.
Do metod niesterowanych zaliczamy:
- Przeciski pneumatyczne tzw. krety (Pneumatic Piercing, Pneumatic Moling)
- Wbijanie rur stalowych (Pipe Ramming)
- Przewierty poziome niesterowane (Horizontal Auger Boring)
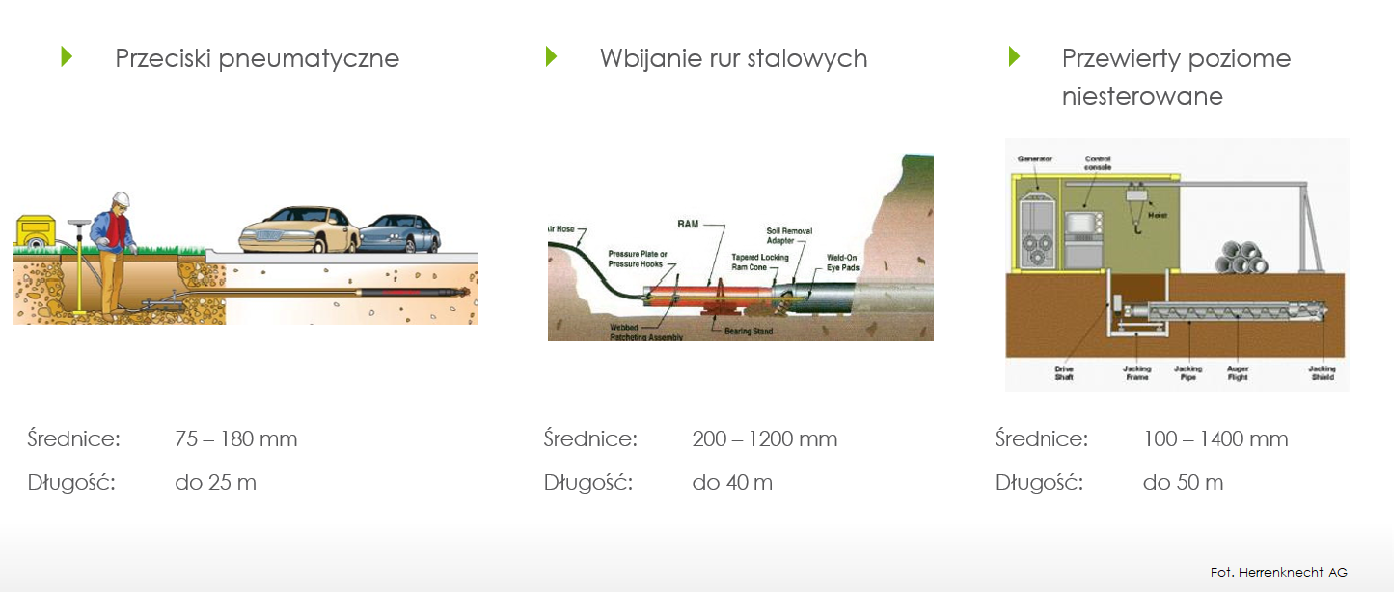
Z kolei do metod sterowanych można zaliczyć:
- Przewierty poziome sterowane (Guided Auger Boring)
- Horyzontalne wiercenia kierunkowe (HDD – Horizontal Directional Drilling)
- Mikrotunelowanie (Microtunneling)
- DSPT (Direct Pipe)
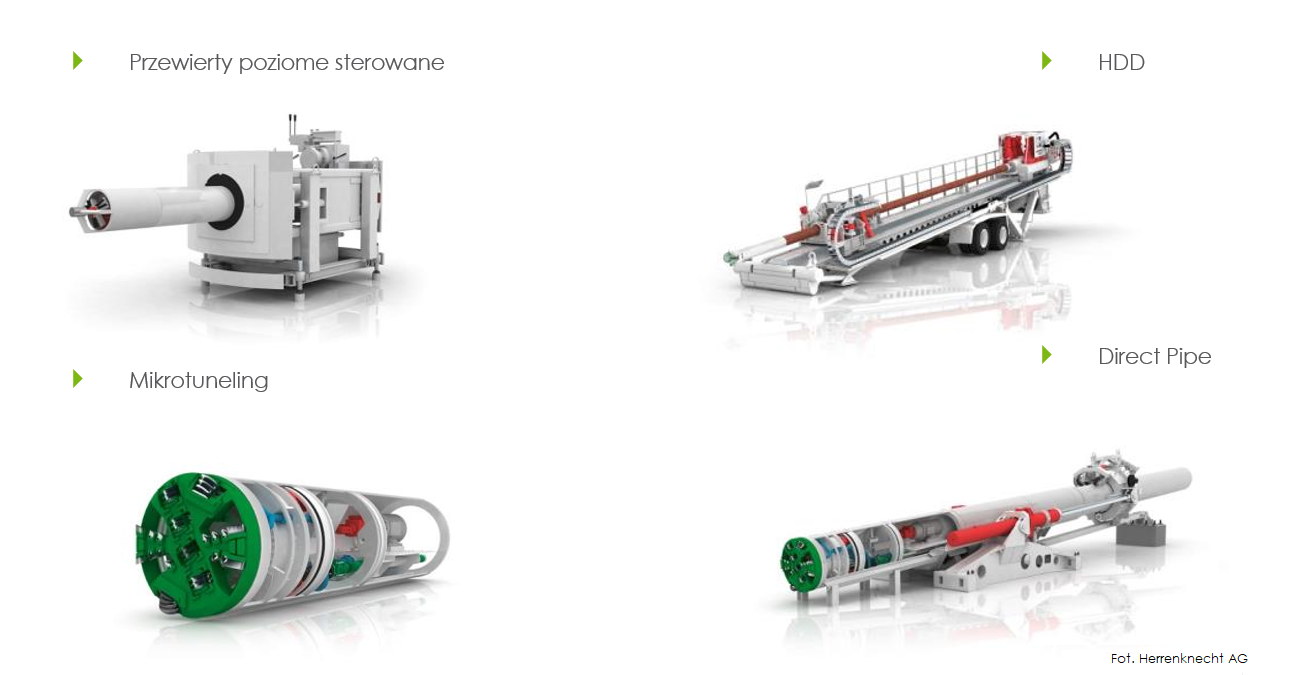
PODZIAŁ METOD ZE WZGLĘDU NA DŁUGOŚĆ INSTALACJI
Jednym z bardziej praktycznych i często stosowanych kryteriów klasyfikacji metod bezwykopowych jest długość instalowanego odcinka. Długość ma bezpośredni wpływ na dobór technologii ze względu na wymagania sprzętowe, logistyczne oraz możliwości kontroli trajektorii przewiertu.
W tym ujęciu metody bezwykopowe dzielimy na:
- Metody krótkodystansowe – stosowane przy realizacjach do ok. 100 metrów. Do tej grupy zalicza się m.in. przewierty poziome, pipe reaming oraz mikrotunelowanie w swojej podstawowej wersji. Są to technologie wykorzystywane najczęściej przy przejściach pod drogami, torami czy innymi przeszkodami terenowymi.
- Metody długodystansowe – wykorzystywane do instalacji na długościach powyżej 100 metrów, często nawet do kilku kilometrów. Do tej grupy zaliczamy mikrotunelowanie większymi średnicami z zastosowaniem stacji pośrednich, wiercenia kierunkowe HDD oraz technologię DSPT (DP). Pozwalają one na realizację zadań inżynieryjnych w złożonych warunkach terenowych, przy jednoczesnym zachowaniu wysokiej precyzji i minimalnej ingerencji w powierzchnię terenu.
Taki podział, choć uproszczony, stanowi przydatne narzędzie wstępnego doboru technologii do wymagań projektowych i uwarunkowań terenowych.
METODY KRÓTKODYSTANSOWE
KRYTERIA WYBORU – EKONOMIA I WARUNKI TECHNICZNE
Wybór odpowiedniej metody bezwykopowej powinien być podyktowany zarówno względami ekonomicznymi, jak i technicznymi. Z perspektywy Inwestora oraz Wykonawcy, metody najprostsze technologicznie – takie jak przeciski pneumatyczne czy wbijanie rur – są zazwyczaj najbardziej ekonomiczne. Cechują się one niskimi kosztami sprzętowymi, krótkim czasem realizacji oraz minimalnym zapotrzebowaniem na specjalistyczną obsługę.
Jednak optymalizacja kosztów i czasu realizacji nie może być jedynym kryterium wyboru technologii. Ostateczna decyzja powinna być poprzedzona szczegółową analizą szeregu czynników, które mogą istotnie wpłynąć na powodzenie całego przedsięwzięcia. Do najważniejszych z nich należą:
- Rodzaj instalowanego medium – np. przewód kablowy, wodociąg, gazociąg czy kanał sanitarny
- Średnica instalacji – występują ograniczenia urządzeń wiertniczych
- Długość i głębokość odcinka – techniczne możliwości niektórych metod są ograniczone zasięgiem lub zakresem głębokości pracy
- Materiał instalowanej rury – niektóre technologie narzucają ograniczenia dotyczące rodzaju i sztywności przewodu;
- Wymagana dokładność wykonania – istotna w przypadku kanałów grawitacyjnych oraz przy pracach w pobliżu istniejącej infrastruktury
- Warunki gruntowo-wodne – obecność gruntów np. nawodnionych, może wykluczać stosowanie metod z otwartymi głowicami
Prawidłowe zidentyfikowanie technik wiercenia poprzez uwzględnienie powyższych aspektów pozwala na wybór metody najbardziej adekwatnej do danego zadania, minimalizując ryzyko niepowodzenia, awarii lub nieprzewidzianych kosztów w trakcie realizacji inwestycji.
METODY DŁUGODYSTANSOWE
KRYTERIA WYBORU – EKONOMIA I WARUNKI TECHNICZNE
Wybór metody bezwykopowej dla instalacji długodystansowych wymaga indywidualnego podejścia projektowego, ponieważ każda z technologii charakteryzuje się odmiennym sposobem realizacji otworu wiertniczego oraz różną geometrią trajektorii. Różnice te mają istotny wpływ na możliwości techniczne, precyzję prowadzenia przewiertu oraz dostosowanie technologii do warunków gruntowo-wodnych i otoczenia inwestycji.
Na schemacie poniżej przedstawiono porównanie typowych trajektorii przewiertów wykonywanych metodą HDD (Horizontal Directional Drilling), Direct Pipe (DSPT) oraz mikrotunelowania, co pozwala zobrazować różnice w sposobie prowadzenia otworu i wynikające z tego ograniczenia lub zalety
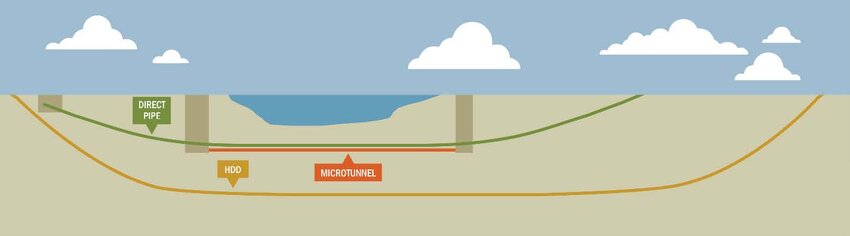
Ponadto, każda z metod posiada określony zakres optymalnych zastosowań pod względem długości instalacji i średnicy rurociągu. Rekomendowane długości pojedynczych instalacji w zależności od średnicy zewnętrznej przewodu mogą determinować konieczność stosowania rur osłonowych co może nie być pożądanym elementem w przypadku zabudowy na długich dystansach.
Wybór odpowiedniej metody powinien być oparty przede wszystkim na analizie ryzyk technicznych, a dopiero w dalszej kolejności na uwarunkowaniach ekonomicznych. Ze względu na skalę przedsięwzięcia, potencjalne konsekwencje niewłaściwego dopasowania technologii do warunków terenowych mogą prowadzić do poważnych awarii, trudnych i kosztownych do naprawy.
Z punktu widzenia Projektanta przekroczenia, kluczowe jest uwzględnienie następujących aspektów:
- Rodzaj gruntu i obecność przeszkód naturalnych
- Dostępność przestrzeni technologicznej – wielkość placów budowy
- Wymagana dokładność trajektorii
- Ryzyko oddziaływania na środowisko – w tym zagrożenie szczelinowanie płuczki
- Długość i średnica instalacji – wpływająca na dobór odpowiednich urządzeń
Ostateczny wybór potwierdzony zostaje szczegółową analizą techniczno-środowiskową oraz oceną dostępnych wariantów przestrzennych, uwzględniającą zarówno ograniczenia terenowe, jak i możliwość zapewnienia bezpieczeństwa operacji wiertniczych. W przypadku długich przekroczeń, gdzie margines błędu jest niewielki, ryzyko techniczne powinno być traktowane jako kluczowe kryterium decyzyjne, nawet jeśli prowadzi to do wyboru rozwiązania droższego w realizacji.
TRAJEKTORIA WIERCENIA
Profil wiercenia to szczegółowy rysunek projektu bezwykopowego, który przedstawia informacje przestrzenne, geologiczne i topograficzne, takie jak granice własności (dzierżawy), obszary wrażliwe środowiskowo, uzbrojenie terenu nad i podziemne. Profil jest niezbędny, nie tylko do prawidłowego zaplanowania i przeprowadzenia wiercenia, ale również stanowi narzędzie komunikacji i wizualizacji. Dla Wykonawcy i Inwestora stanowi podstawę do opracowania kosztorysu i zaplanowania budżetu.
Przy projektowaniu trajektorii otworu podstawowymi parametrami są:
- Sekcja wejścia i wyjścia – pierwszy i ostatni odcinek osi przewiertu powinien być prostoliniowy (bez zmian kątowych), ponieważ w tych miejscach występuje niewielka miąższość nadkładu (przykrycia). Długość tych odcinków należy dostosować do rozmiaru otworu oraz masy i sztywności głowicy wiercącej.
- Kąt wejścia i wyjścia – określa odchylenie trajektorii otworu w punktach wejścia i wyjścia narzędzia wiercącego względem poziomu odniesienia. Optymalne wartości zależą od zastosowanej technologii, typu maszyny oraz materiału instalowanego rurociągu.
- Promień krzywizny – promień łuku dla rurociągów stalowych zależy od ich średnicy, grubości ścianki oraz współczynnika wyznaczanego na podstawie charakterystyki gruntu. W przypadku rur PEHD promień krzywizny określany jest przede wszystkim przez minimalny promień gięcia żerdzi wiertniczych.
- Głębokość posadowienia – przy planowaniu głębokości prowadzenia otworu należy uwzględnić możliwe osiadanie terenu wynikające z usunięcia gruntu, odprężenia podłoża oraz działających obciążeń, w tym dynamicznych.
W przypadku przewiertów prowadzonych po łukach pionowych (HDD, DSPT, rzadziej mikrotunelowanie), należy uwzględnić ryzyko szczelinowania hydraulicznego płuczki wiertniczej, prowadzącego do jej wypływu na powierzchnię terenu. Głębokość rurociągu powinna być tak zaprojektowana, aby zapobiegać niekontrolowanemu wyciekowi płuczki, z uwzględnieniem wytrzymałości gruntu i dopuszczalnych ciśnień.Ciśnienie w otworze zależy od ciśnienia hydrostatycznego cieczy wypełniającej (w przypadku HDD), oporów przepływu lub ciśnienia tłoczenia (w technologiach MT i DSPT).
W technologii HDD, dla zapewnienia skutecznego transportu urobku od ściany otworu do urządzenia wiertniczego, prawidłowa cyrkulacja płuczki powinna być utrzymywana na możliwie najdłuższym odcinku – co najmniej 75% całkowitej długości przewiertu.
Miejsce potencjalnego szczelinowania należy lokalizować poza przekraczanymi przeszkodami, w miejscach, gdzie ewentualny wypływ płuczki nie spowoduje istotnych utrudnień ani zagrożeń środowiskowych lub infrastrukturalnych.W przewiertach realizowanych metodą DSPT i mikrotunelowania, szczelinowanie może występować głównie w przypadku znacznych różnic wysokości terenu. Choć urobek transportowany jest w tych technologiach wewnątrz stalowych rur, co zmniejsza skutki szczelinowania, brak ciągłości smarowania pobocznicy może prowadzić do wzrostu sił instalacyjnych.
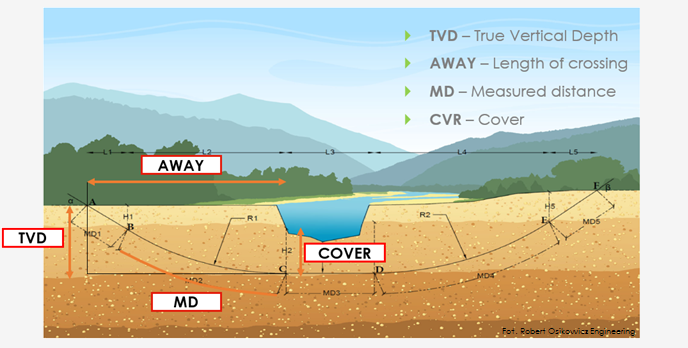
ANALIZA CIŚNIEŃ WGŁĘBNYCH
Przy doborze głębokości posadowienia rurociągu należy uwzględnić szereg czynników technicznych, geologicznych i eksploatacyjnych, które determinują bezpieczne i efektywne przeprowadzenie instalacji, takich jak ukształtowanie terenu i jego spadki, rodzaj i stan gruntu, występowanie przeszkód podziemnych i naziemnych, ryzyko osiadania lub przemieszczeń gruntu, czy wymogi formalne i środowiskowe.
Głębokość posadowienia powinna także uwzględniać nośność gruntów i skał oraz zapobiegać ucieczkom płuczki wiertniczej. Ciśnienie panujące w otworze zależy od ciśnienia hydrostatycznego cieczy wypełniającej otwór oraz od oporów przepływu.
Opory przepływu w poszczególnych elementach systemu cyrkulacyjnego zależą od:
− właściwości przepływającej cieczy (model reologiczny),
− geometrii i właściwości fizycznych elementów systemu,
− reżimu przepływu (laminarnego, tłokowego lub turbulentnego).
Analiza ciśnień dynamicznych porównywana jest z teoretyczną wytrzymałością gruntu. Pozwala to określić prawdopodobieństwo oraz potencjalne miejsca na trasie przewiertu, w których może dojść do przerwania ciągłości warstw gruntu i przedostania się płuczki wiertniczej na powierzchnię terenu (tzw. „frack-out”).
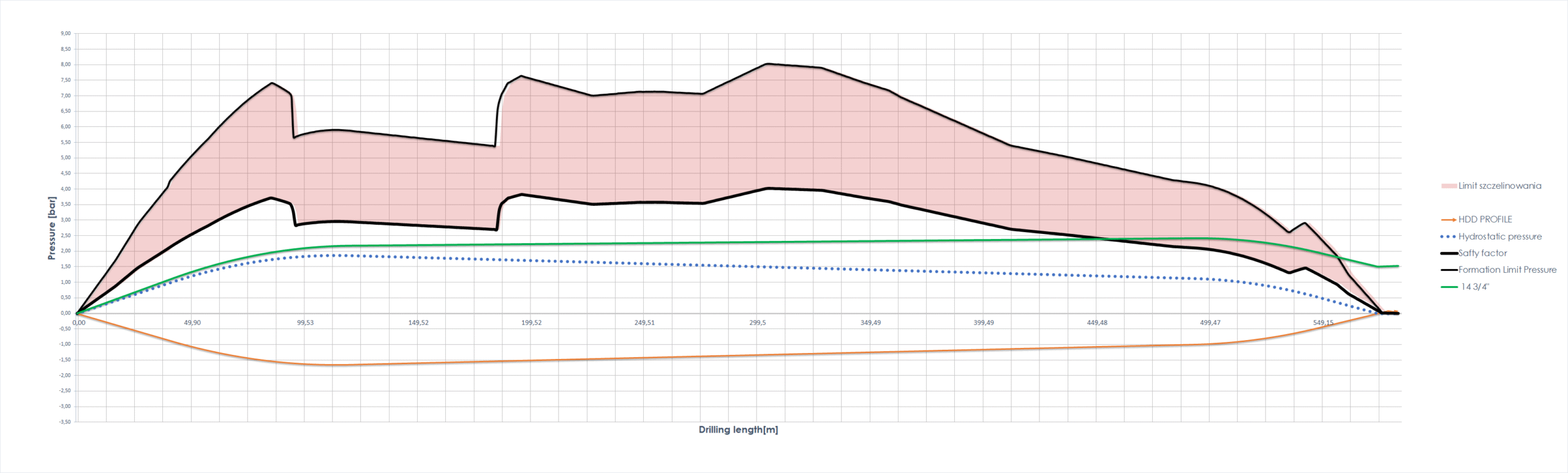